Qu’est-ce que le Poka Yoke, méthode anti-erreur ?
Le Poka Yoke, ou démarche Poka Yoke, est une méthode de contrôle qualité développée au Japon dans les années 60. Elle vise à prévenir les erreurs et à éliminer les défauts dès la source.
- 1 Qu’est-ce que le Poka Yoke
- 2 Comment mettre en place la méthode Poka Yoke dans votre atelier
- 3 Application de la méthode Poka Yoke avec le logiciel Aquiweb
Dans cet article, nous allons explorer en détail ce qu’est la démarche Poka Yoke. Comment fonctionne-t-elle, et pourquoi elle est importante pour les entreprises qui cherchent à améliorer leur efficacité et leur rentabilité.
Qu’est-ce que le Poka Yoke ?
Poka Yoke : définition
Le terme Poka Yoke signifie littéralement « faire en sorte qu’il n’y ait pas d’erreurs ». Il s’agit d’une méthode de contrôle qualité qui vise à éviter les erreurs de production en utilisant des dispositifs de prévention ou de détection des erreurs. C’est l’ingénieur japonais Shigeo Shingo qui a développé cette méthode, après avoir travaillé pour Toyota dans les années 60.
La démarche Poka Yoke est basée sur le principe selon lequel il est plus facile et moins coûteux de prévenir les erreurs dès le départ plutôt que de les corriger une fois qu’elles se sont produites. Aussi, elle implique l’utilisation de dispositifs qui aident les opérateurs à éviter les erreurs de production en leur fournissant des signaux clairs et des instructions précises.
Elle est une des méthodes les plus utilisées du Lean Manufacturing, concept lui aussi originaire du Japon dans les années 60.
Comment fonctionne la démarche Poka Yoke ?
La démarche Poka Yoke repose sur deux types de dispositifs :
- Dispositifs de prévention, conçus pour empêcher les erreurs de se produire.
- Dispositifs de détection, conçus pour détecter les erreurs une fois qu’elles se sont produites.
Les dispositifs de prévention sont généralement plus efficaces que les dispositifs de détection, car ils aident à éviter les erreurs dès le départ. Ils peuvent alors prendre la forme de guides, de gabarits, de détrompeurs ou de verrous. Par exemple, un détrompeur empêche un opérateur de connecter deux pièces dans le mauvais sens.
Les dispositifs de détection, quant à eux, détectent les erreurs qui ont échappé aux dispositifs de prévention. Ils peuvent alors prendre la forme de capteurs, de voyants lumineux ou de sons d’alarme. Par exemple, un voyant lumineux s’allume pour signaler qu’un produit a été mal assemblé.
Pourquoi la démarche Poka Yoke est-elle importante pour les entreprises ?
La démarche Poka Yoke est importante pour les entreprises, car elle permet d’améliorer la qualité des produits tout en réduisant les coûts de production.
En effet, en prévenant les erreurs dès le départ, les entreprises peuvent éviter les coûts liés à la correction des erreurs. Parmi ces coûts, nous retrouvons le plus souvent les coûts de main-d’œuvre, les coûts de matériel et les coûts de temps.
Exemples d’erreurs fréquentes en atelier industriel à corriger avec le Poka Yoke
Comme nous l’avons vu, les erreurs peuvent avoir des conséquences désastreuses pour la qualité des produits et la rentabilité de l’entreprise. La méthode Poka-Yoke, ou méthode « anti-erreur », vise à prévenir les erreurs et les défauts dès la source. Voici quelques-unes des erreurs les plus fréquentes :
1 Les erreurs d’opérations
Les erreurs d’opération sont courantes en atelier industriel et peuvent entraîner des défauts de fabrication. Par exemple, si un composant est mal positionné lors de l’assemblage, si une opération est manquée ou si l’opérateur à mal effectué une opération, cela entraîne des problèmes de fonctionnement ou une mauvaise qualité de finition.
Le Poka-Yoke prévient ces erreurs en utilisant des gabarits ou des détrompeurs. Ceux-ci guident les opérateurs dans le positionnement correct des composants.
2 Les erreurs de montage
Dans un atelier, des opérateurs inexpérimentés ou ayant une mauvaise formation peuvent faire des erreurs de montage. Cela peut entraîner des problèmes de fonctionnement ou une mauvaise qualité de finition.
Le Poka-Yoke utilise des guides de montage, des formes spécifiques ou des codes couleur qui indiquent l’ordre correct de montage.
3 Les erreurs de configuration
Elles peuvent être causées par des erreurs humaines lors du réglage de l’équipement, mais aussi par les mauvaises dimensions d’une pièce fournie par un fournisseur.
Le Poka-Yoke prévient ces erreurs en utilisant des capteurs ou des dispositifs de mesure automatiques qui détectent les écarts par rapport aux spécifications.
4 Les erreurs de sélection pièce/outil
Les erreurs de sélection peuvent être causées par des opérateurs qui choisissent le mauvais composant ou le mauvais outil pour la tâche à effectuer.
Le Poka-Yoke prévient ces erreurs en utilisant des guides de sélection ou des étiquettes de code couleur qui indiquent le composant ou l’outil correct à utiliser.
5 Les erreurs de contrôle qualité
Les erreurs de contrôle qualité peuvent être causées par des erreurs humaines lors du contrôle qualité manuel ou des équipements de contrôle qualité défectueux. Cela peut entraîner des problèmes de qualité des produits ou une non-conformité aux spécifications.
Le Poka-Yoke prévient ces erreurs en utilisant des capteurs ou des dispositifs de mesure automatiques qui vérifient que les produits sont conformes aux spécifications.
6 Les erreurs de pièces manquantes
Toutes les pièces ne sont pas incluses dans l’assemblage, le montage, par manque d’accessibilité ou par oubli.
Le Poka-Yoke prévient ces erreurs en utilisant des « Kits » de montage dans lesquels l’ensemble des pièces nécessaires à la fabrication d’un produit sont présentes et positionnées de manière ludique.
Exemples de Poka Yoke
Pick to light :
En industrie, le système de Pick to light désigne la procédure d’opération assistée, qui consiste à guider l’opérateur vers une pièce à prélever (Pick) et utiliser à l’aide de lumière (light) qui s’allume à l’endroit où se situe le produit à prélever.
Détrompeur :
Il existe bons nombres de systèmes de détrompeurs, mais le plus courant est le détrompage par guide mécanique, qui consiste à empêcher l’assemblage de pièces dans la mauvaise position.
Par exemple, une clé de montage qui ne peut être insérée que dans un sens spécifique ou des connecteurs électriques qui ne peuvent être insérés que dans la bonne orientation.
Kitting :
Le kitting consiste à réunir dans un « Kit » l’ensemble des éléments nécessaires à la réalisation d’une tâche. Ainsi, l’opérateur a à disposition toutes les pièces à assembler, et ne peut pas en oublier.
Capteurs :
Les capteurs sont des dispositifs qui détectent les écarts par rapport aux spécifications et avertissent l’opérateur en cas de problème.
Par exemple, un capteur de pression qui détecte une pression anormalement élevée dans une machine ou un capteur de présence qui vérifie si tous les composants nécessaires sont présents avant de lancer une opération.
Gabarit de contrôle :
Les gabarits de contrôle vérifient si les pièces ou les composants ont été fabriqués ou assemblés correctement.
Par exemple, un gabarit de contrôle pour vérifier si les trous de montage sont correctement alignés ou si les dimensions des pièces sont correctes.
Codes couleur :
Les codes couleur sont des dispositifs qui indiquent l’ordre ou la correspondance des pièces ou des composants.
Par exemple, des étiquettes de couleur pour indiquer les tailles de boulons et d’écrous à utiliser.
Alarmes sonores ou lumineuses :
Les alarmes sonores ou lumineuses sont des dispositifs qui alertent les opérateurs lorsqu’une erreur se produit.
Par exemple, une alarme qui se déclenche lorsque la pression de la machine dépasse un certain seuil ou un voyant qui s’allume lorsque tous les composants ne sont pas présents.
Dispositifs de sécurité :
Les dispositifs de sécurité empêchent une machine de fonctionner si une opération n’a pas été effectuée correctement ou si tous les composants nécessaires ne sont pas en place.
Par exemple, un dispositif qui empêche une machine de démarrer si la porte d’accès n’est pas fermée ou si le capot de protection n’est pas en place.
Comment mettre en place la méthode Poka-Yoke dans votre atelier ?
Nous allons vous voir comment mettre en place la méthode Poka-Yoke dans votre atelier en suivant les principes d‘amélioration continue pour améliorer la qualité de vos produits et augmenter votre rentabilité.
Les différents niveaux de Poka-Yoke
Le Poka-Yoke (ou contrôle des erreurs) possède trois niveaux d’application. Pour comprendre les différents niveaux de Poka-Yoke, nous prendrons un exemple industriel suivi de l’exemple d’une voiture.
Niveau 1 : Séquentiel
Le niveau 1 du Poka-Yoke est le moins stricte. Il vise à empêcher l’unité produite défectueuse d’atteindre l’opération suivante, ou le client.
Par exemple, l’opérateur devra suivre et remplir des feuilles d’inspection ou des listes de contrôles à effectuer. En ce sens, il n’empêche pas les erreurs mais aide à les identifier, les contrôler et les corriger.
Dans le cas de la voiture, le contrôle technique ressemble au niveau 1. Le garagiste fait des contrôles et s’assure que tout aille bien. Dans le cas contraire, il signale les défauts à corriger et effectuera les réparations pour pouvoir réparer votre véhicule.
Niveau 2 : Informatif
Le niveau 2 lui, considéré comme le « niveau d’avertissement », détecte et fournit une notification (lumière, sons, etc…) à l’opérateur quand une condition est respectée ou pas.
Par exemple, cela peut être une lumière verte ou rouge sur un outil dynamométrique selon que le couple correct est atteint ou pas. Ou une lumière qui indique quel outil utiliser sur une étagère.
Dans une voiture, le niveau 2 du Poka-Yoke est très présent. Lorsque vous oubliez de mettre la ceinture, un signal sonore et lumineux vous avertit de cet oubli. Pareil lorsqu’il est temps d’aller faire le plein de carburant.
Niveau 3 : Physique
Le niveau 3 du Poka-Yoke est le plus strict. Il vise à empêcher toute erreur possible de la part de l’opérateur. S’il est bien mis en place, aucune pièce non-conforme ne peut être produite.
Par exemple, des dispositifs d’assemblage et de gabarit qui ne se mettent que dans un seul sens pour éviter toute erreur.
Sur les voitures récentes, les constructeurs choisissent d’appliquer le niveau 3 du Poka-Yoke pour assurer la sécurité de tous. Pour éviter un déplacement involontaire, les constructeurs imposent aux conducteurs de voitures manuelles d’appuyer sur la pédale d’embrayage, avant de démarrer le moteur. Les voitures automatiques, elles, doivent être en position parking (ou neutre) pour démarrer. Le non-respect de ces conditions empêche le démarrage de la voiture.
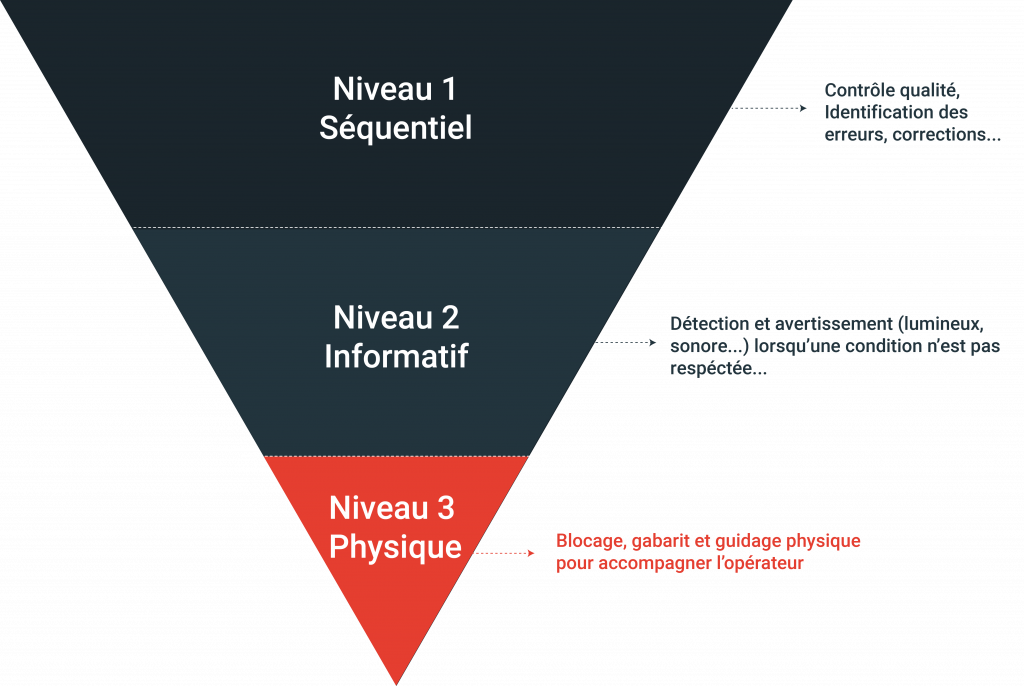
La mise en place de la méthode Poka Yoke
1 Analysez le processus de production
Premièrement, mettre en place la méthode Poka-Yoke dans votre atelier consiste à analyser votre processus de production.
Il est important de comprendre où les erreurs se produisent et pourquoi. Cette analyse vous aidera à identifier les zones à risque et les étapes du processus qui nécessitent une attention particulière.
2 Identifiez les sources d’erreurs
Après avoir analysé votre processus de production, vous pouvez identifier les sources d’erreurs. Cela peut inclure des erreurs humaines telles que la confusion ou la fatigue. Mais aussi des problèmes d’équipement tels que des outils défectueux, ou des problèmes de communication.
3 Concevez des dispositifs de prévention
La méthode Poka-Yoke repose sur l’utilisation de dispositifs de prévention pour empêcher les erreurs de se produire. Notons que ces dispositifs peuvent prendre la forme de guides, de détrompeurs, de gabarits ou de verrous. Il est important de concevoir des dispositifs qui sont faciles à utiliser et à comprendre pour les opérateurs.
4 Concevez des dispositifs de détection
En plus des dispositifs de prévention, il est également important de concevoir des dispositifs de détection pour détecter les erreurs qui se produisent malgré les dispositifs de prévention. Ces dispositifs peuvent prendre la forme de capteurs, de voyants lumineux ou de sons d’alarme. Il est important de s’assurer que les opérateurs peuvent rapidement et facilement réagir en cas d’erreur détectée.
5 Mettez en place des formations et des procédures
La mise en place de la méthode Poka-Yoke nécessite une formation et des procédures pour les opérateurs. Il est important de s’assurer que les opérateurs comprennent les dispositifs de prévention et de détection et qu’ils sont formés à leur utilisation. Il est également important de mettre en place des procédures claires pour la gestion des erreurs détectées.
6 Testez et évaluez votre système Poka Yoke
Enfin, une fois que vous avez mis en place la méthode Poka-Yoke, il est important de tester et d’évaluer votre système. Ainsi, vous vous assurez qu’il fonctionne correctement. Vous pouvez effectuer des tests de validation pour vous assurer que les dispositifs de prévention et de détection fonctionnent comme prévu et que les opérateurs sont formés à leur utilisation.
Application de la méthode Poka-Yoke avec le logiciel Aquiweb
Après avoir vu les 6 étapes pour mettre en place la méthode Poka-Yoke dans votre atelier, nous allons voir comment le logiciel MES Aquiweb vous accompagne dans cette mise en place (voir Pourquoi intégrer un logiciel MES dans votre atelier industriel).
1 Aquiweb vous aide à analyser votre processus de production
Premièrement, comme nous l’avons vu précédemment, la première chose à faire dans une méthode Poka-Yoke est d’analyser le processus de production. Aquiweb simplifie et digitalise cette analyse en temps réel. Les IIoT, capteurs sur vos lignes et opérateurs communiquent avec le logiciel MES sur tous les évènements qui apparaissent dans l’atelier. Ainsi, des graphiques, diagrammes, données numéraires transmettent et illustrent les données collectées.
2 Aquiweb vous aide à identifier les sources d’erreurs
Deuxièmement, la méthode Poka-Yoke cherche à réduire les erreurs dans le processus de fabrication. C’est pourquoi il est indispensable de les identifier. En ce sens, Aquiweb fait ressortir des analyses sur les différentes causes responsables d’erreurs.
Ces analyses aident à mettre en évidence les endroits précis où les erreurs interviennent, et d’en comprendre les causes. Vous pouvez ainsi découvrir les goulots d’étranglement, les causes fréquentes de rebuts, les causes fréquentes de pannes… Et ainsi agir pour anticiper et réduire toutes ces erreurs qui pénalisent la production.
3 Aquiweb vous aide à mettre en place des dispositifs de prévention
Par exemple :
Digitaliser les OF (démarche informative)
La digitalisation des ordres de fabrication vise à réduire les erreurs humaines, en apportant l’ensemble des éléments de l’OF (lancement du bon OF au bon moment, affichage des informations, spécificités du produit, les quantités à réaliser, les matériaux à utiliser…).
Documentation (démarche informative)
En digitalisant la documentation (directement en lien avec l’ERP), le manager s’assure non seulement que l’opérateur dispose de la bonne documentation à jour, mais aussi l’accès direct et simplifié à cette documentation au poste opérateur, en un clic.
Ok démarrage (démarche séquentielle)
Aquiweb propose une checklist personnalisable de points à valider avant de lancer une opération ou une action sur la production. Ces points à valider permettent de s’assurer de l’état de la production et du maintien des conditions optimales dans le but de réduire les erreurs.
4 Aquiweb vous aide à mettre en place des dispositifs de détection
Par exemple :
Imposer les contrôles qualité avec des éléments obligatoire à remplir (démarche séquentielle)
Pour détecter toute erreur susceptible de dégrader la production, Aquiweb est capable d’imposer des contrôles qualité périodique (toutes les x pièces, toutes les x minutes…). Dans une démarche séquentielle, une valeur non renseignée peut bloquer le contrôle qualité et bloquer la production.
IIoT, capteurs (démarche informative)
Pour détecter au plus vite les dégradations de production, Aquiweb communique avec l’ensemble des capteurs de l’atelier. Ainsi, les conditions de production comme la température, l’humidité, la qualité, les rebuts, la cadence de production et bien d’autres font l’objet d’un suivi précis qui, en cas de dépassement alerte immédiatement l’opérateur et le manager.
5 Aquiweb vous aide à former vos opérateurs et mettre en place des procédures
Le paramétrage d’Aquiweb permet l’affichage de messages types en fonction des erreurs rencontrées pour accompagner vos opérateurs dans la gestion des erreurs. Mais aussi pour mettre en place des procédures de redémarrage de ligne etc…
Afin de s’assurer du bon déroulement de la méthode Poka-Yoke, vous pouvez former vos opérateurs à l’aide d’Aquiweb lors de réunions AIC, ou à travers la diffusion d’informations sur les différents écrans de l’atelier.
6 Aquiweb vous aide à tester et analyser votre démarche Poka Yoke
Enfin, avec les analyses et indicateurs proposés par Aquiweb, vous pouvez comparer les résultats actuels (après la mise en place du Poka-Yoke), avec les résultats antérieurs (avant la mise en place du Poka-Yoke).