Comment gagner du temps dans la gestion de votre atelier ?
L’industrie se transforme et se complexifie au fil du temps : plus exigeante, plus compétitive et plus flexible. Les acteurs de l’atelier sont aujourd’hui exposés à de nouveaux enjeux : un échange de données constants, un management collaboratif, une transformation digitale des outils de gestion, un monitoring en temps réel des activités de l’usine. Parallèlement, on trouve des clients de plus en plus exigeants, qui souhaitent des produits innovants et de qualité, au moindre coût, disponibles au plus tôt, …
Des outils et des méthodes très simples permettent aujourd’hui de gagner du temps dans la gestion de votre atelier : c’est ce que nous allons découvrir dans cet article.

La gestion de l’atelier : quelles sont les problématiques observées ?
Dans la gestion d’un atelier, le manager est souvent confronté à une liste de problèmes qui ne cesse d’augmenter et qui pose des questions au responsable de production :
- Je n’ai pas les données de ma production en temps réel mais plutôt le lendemain ou le surlendemain
- Je passe beaucoup de temps à saisir des données sur l’outil informatique qui proviennent de saisies manuelles des acteurs en production (opérateurs, techniciens, …)
- Je ne peux pas garantir la fiabilité des données
- Je n’ai pas d’indicateur pour évaluer la performance de ma production
- Je n’ai aucun moyen de planifier mes opérations de production
- Je ne peux pas suivre l’activité de l’usine lorsque je suis en déplacement
Optimiser la gestion des données de production et des informations dans l’usine permet de gagner du temps dans la gestion d’un atelier et implique un processus de transformation digitale pour entrer dans l’usine du futur.
Evaluer les pertes dans l’atelier : comment ?
Les pertes dans l’atelier sont liées à plusieurs facteurs connus par tous les responsables de production : manque de suivi opérationnel, difficulté de planifier la production et de suivre l’exécution des opérations, pertes de temps liées à des tâches administratives, difficulté d’évaluer la performance, pertes de fiabilité des informations qui navigue entre les acteurs, pas d’historique des échanges entre les managers et les opérateurs, …
Avec le logiciel MES, toutes les informations de l’atelier sont extraites automatiquement des moyens (machines et systèmes de gestion) et/ou manuellement auprès des acteurs. Le MES (Manufacturing Execution System) collecte, analyse, consolide et affiche les données en temps réel à la bonne personne ou au bon service. Cela permet de gagner du temps dans la recherche des données, la saisie informatique, la consolidation par des calculs, des comparaisons, des graphiques, et le stockage qui se fait automatiquement sur un serveur interne ou un cloud. Toutes les actions à non-valeurs ajoutées sont supprimées : le responsable de production peut consacrer plus de temps à l’amélioration continue de son atelier.
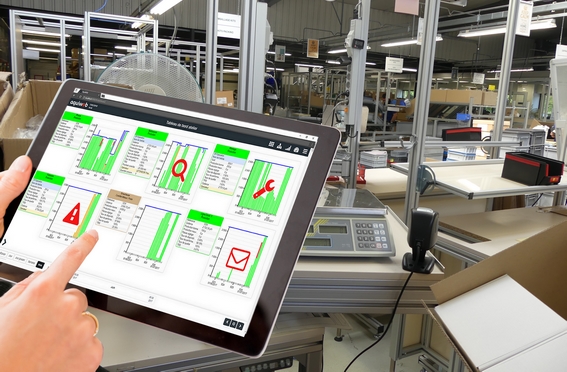
Supprimer le papier dans l’atelier : pourquoi ?
Le papier prend encore une place omniprésente dans l’environnement industriel actuel. Par exemple, on retrouve encore très souvent, chez de nombreux sites industriels de toutes tailles, des documents papiers : plans de contrôles, fiches suiveuses, fiches de non-conformité, diagnostic maintenance, relevés de production, …
Pourquoi passer son atelier au zéro papier ?
Le papier n’est pas un support durable. Son utilisation nécessite une certaine logistique qui ne peut se faire sans l’homme. Dans un contexte d’une usine, je lance l’impression, je le complète manuellement (ci-besoin), et je l’affiche dans l’atelier auprès des postes concernés, et je le modifie constamment suite aux différentes mises à jour réalisées. Dans l’atelier, les documents papiers sont susceptibles de s’abîmer, de se déchirer, de se perdre (dans le cadre d’une mobilité des acteurs dans l’atelier).
Il a ensuite un véritable coût financier dans l’approvisionnement en papier, l’utilisation d’imprimantes (coût d’achat, maintenance, …) et le stockage (archives externes, rangements dans les bureaux, …).
Enfin, l’impact de l’activité des entreprises sur l’environnement est au cœur des problématiques actuelles. Les enjeux de Responsabilité Sociétales des Entreprises (RSE) incluent le développement durable dans son bon respect. Les entreprises deviennent labellisées, normées et développent leurs images à travers ces actions.
Quelle solution de substitution au papier ?
Le numérique remplace le papier dans l’atelier. Le logiciel MES digitalise toutes les informations liées à la production : relevés des états machines, indicateurs de performance, documentation en atelier, procédures qualité, fiches de suivi, plans de contrôle, instructions de travail, …
Avec de simples paramétrages et en quelques clics, les opérateurs disposent sur un seul écran de toutes les informations nécessaires qui les guident dans leur process. Le technicien maintenance dispose de ses plans de maintenance sur sa tablette et peut se déplacer facilement avec pour réaliser ses interventions. Le technicien qualité contrôle sa production sur sa tablette. Il est alerté si les résultats sont non conformes et peut renseigner les non conformités sur sa tablette avec une prise de photo du défaut par exemple.
Finalement, toutes ces informations sont stockées, historisées sur un serveur local ou cloud et sont consultables à tout moment par les managers.
Monitorer l’atelier à distance avec son smartphone : quel est l’intérêt ?
Le logiciel MES permet aux patrons de PME, aux directeurs de la production et /ou directeurs industriels, de gérer en temps réel et à distance les activités de leur usine voir de l’ensemble des sites. Garder un œil sur sa production peut garantir une production juste à temps, permettre d’anticiper les pannes des équipements de production et de communiquer avec ses équipes à tout moment. Objectif : réagir au plus vite à un aléa pour limiter les pertes.
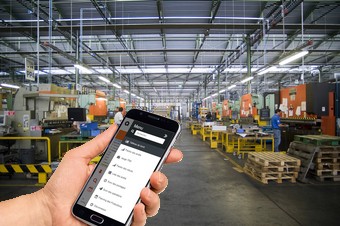
A partir de son smartphone, le responsable consulte à tout moment l’état de ses équipements (en production, à l’arrêt, en panne, en maintenance, …). Il garde un suivi sur ses indicateurs de performance (TRS, TRG, …) et peut alerter en temps réel les équipes sur un atelier ou un poste de travail en laissant un message (plus d’informations sur la mobilité)