Le TRS (Taux de Rendement Synthétique) : définition et calcul
Le taux de rendement synthétique (TRS) est l’indicateur de référence dans l’industrie. Il permet à la fois de connaître le niveau de performance d’un outil de production, et d’apporter des plans d’action pour l’optimiser.
Ainsi, dans bien des cas, le calcul du TRS précède la mise en œuvre d’une démarche d’optimisation de la production sans forcément investir dans de nouveaux moyens de production plus performants. Le taux de rendement synthétique s’intéresse à l’identification des pertes responsables de la non-productivité. Pour améliorer le TRS, il faut d’abord connaître sa composition et les leviers qui l’impacte.
Qu’est-ce que le taux de rendement synthétique (TRS) ?
Définition : Taux de rendement synthétique
Définition : Le taux de rendement synthétique (TRS) est un indicateur normé par l’AFNOR depuis 2002. Il évalue ainsi avec précision la performance d’un équipement industriel. Si le TRS est devenu l’indicateur clé dans l’industrie, c’est parce qu’il représente de manière synthétique le rendement d’un outil de production à travers trois autres indicateurs : taux de disponibilité, taux de performance, et taux de qualité.
La collecte des données nécessaires à la connaissance de ces indicateurs est bien souvent une première étape vers l’amélioration continue.
Pour comprendre, imaginons un atelier industriel idéal avec un TRS de 100% :
L’atelier ne fabrique que des pièces bonnes (taux de qualité 100%), à la cadence maximale théorique de l’outil de production (taux de performance 100%), sans aucun temps d’arrêt non planifié (taux de disponibilité 100%) !
Calcul du rendement de la production
Le TRS fait la lumière sur l’état d’un moyen de production, en utilisant des données précises. Aussi sa composition offre seulement une étude approfondie de la santé du moyen de production. Elle offre également la possibilité de corriger des problèmes trop souvent délaissés par la mise en place de plans d’actions.
Même si le TRS donne une vision globale, sa mesure utilise des données collectées sur chaque ligne ou chaque moyen de production. Elle peut ainsi déterminer les goulots d’étranglement, par exemple. Cependant, sans cette identification et les actions correctives mises en place, un moyen ne pourra jamais produire davantage que ce que permet l’équipement sujet au goulot d’étranglement.
Finalement, dans bien des cas, après avoir calculé le TRS et réalisé des actions d’amélioration continue, les industriels constatent qu’avec le même outil de production, ils peuvent produire autant qu’en investissant dans un deuxième outil.
Augmenter le rendement de la production sans investir dans de nouveaux moyens, là est tout l’intérêt du calcul et de l’amélioration du TRS.
Pour comprendre comment le TRS « dissèque » un moyen de production, analysons les différents temps d’état.
Les temps d’état
Il correspond au temps total de possession du moyen. Temps pendant lequel il est théoriquement utilisable. (24h pour un jour, 168h pour une semaine…), c’est en fait la durée de la période d’analyse.
Ce temps est pendant lequel l’industriel a décidé d’ouvrir le moyen. (1 poste, 2 postes, … sur 5 jours par exemple).
To = temps total – fermeture de l’atelier
Temps pendant lequel le moyen de production est engagé avec la volonté/possibilité de produire selon l’organisation.
Tr = temps d’ouverture – (pause, réunion, maintenance, nettoyage…)
Temps pendant lequel le moyen fabrique des produits.
Tf = temps requis – (pannes, réglages, changements de série…)
Temps de référence pendant lequel le moyen produit dans le respect du temps de cycle de référence. (ou cadence théorique).
Tn = temps de fonctionnement – écarts de cadence
Temps pendant lequel le moyen fabrique des produits de bonne qualité.
Tu = temps net – temps passé à faire de la non-qualité
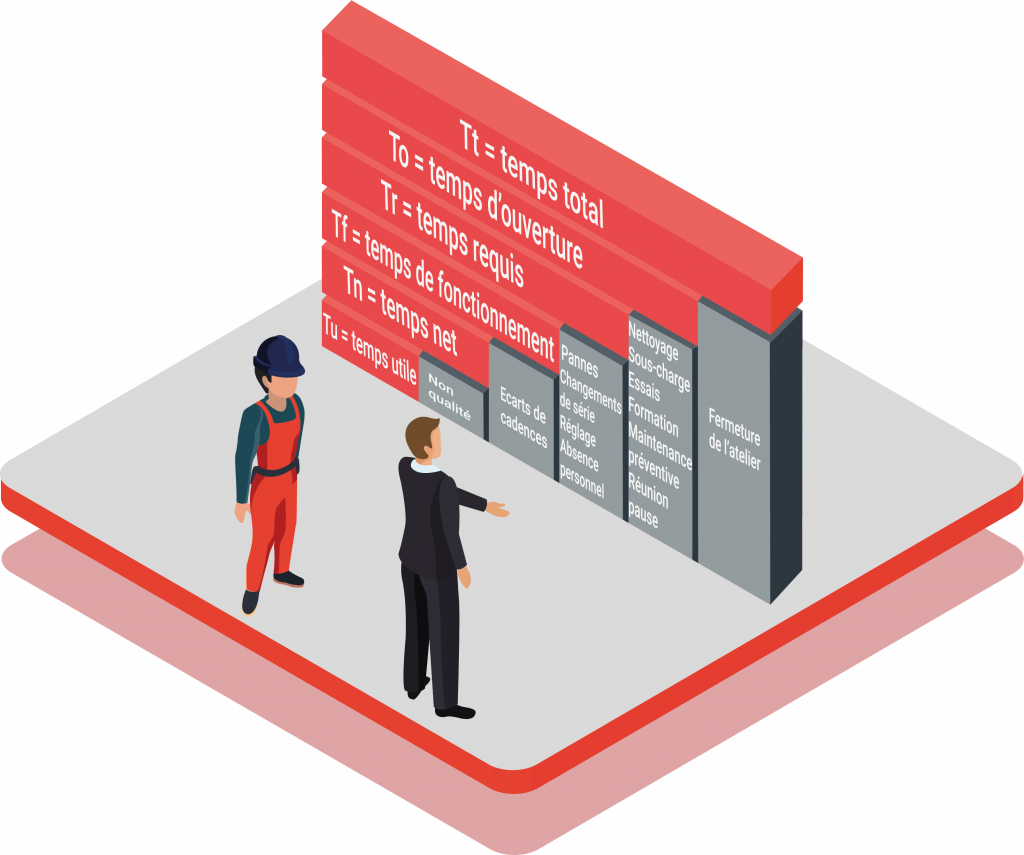
Comment calculer le TRS ?
En fonction des objectifs visés, du mode de production et des éléments disponibles, il y a plusieurs façon de calculer le TRS. Ces façons ne se valent pas toutes car ne nécessitent pas le même degré de connaissance de l’outil, et donc ne fournissent pas le même approfondissement de l’analyse.
Formules simples du TRS
Pour les industriels soucieux de connaître le taux de rendement synthétique de leur moyen de production, mais qui font face à une opacité de ce moyen (souvent induite par un manque de collecte de données ou simplement par des procédés de fabrication spéciaux), deux formules s’offrent à eux.
1. Le ratio des temps d’états pour calculer le TRS
Par souci de simplicité, le TRS a pendant longtemps été calculé en faisant le ratio entre temps passé à fabriquer des produits « bons » à la cadence nominale d’un moyen de production, divisé par le temps d’engagement du moyen. Autrement dit, le moyen le plus simple de calculer le TRS est de diviser le temps utile par le temps requis.
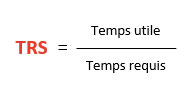
Prenons par exemple un outil de production avec un temps de cycle de référence de 6 minutes (cadence nominale de 10 pièces par heure).
Au bout de 8h, il devrait produire 80 pièces. Mais après vérification, il en a produit 75, dont 70 bonnes, soit un temps utile 70 x 6 minutes, soit 420 minutes
Autrement dit, le moyen de production réalise une pièce bonne en 6.4 minutes au lieu de 6.
Avec cette formule de calcul du TRS, on aura donc ;
TRS = 420 / 480 = 87.5%
Largement utilisée par les industriels pour déterminer le TRS, cette formule trop simpliste n’accorde que trop peu d’intérêt aux causes responsables de la non-productivité.
Pire encore, alors que le temps requis se mesure facilement (temps d’ouverture – arrêts programmés), il est beaucoup plus difficile de calculer le temps utile puisqu’il faut d’abord connaître le temps de cycle de référence (temps utile = quantité bonne x temps de cycle de référence).
2. Les quantités pour calculer le TRS
Encore plus simple, le TRS peut être calculé en faisant le rapport entre la quantité bonne réalisée et la quantité théoriquement réalisable.
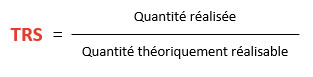
Reprenons notre outil de production capable de produire 10 pièces par heure.
A la fin d’une journée de 8h, l’outil n’a produit cette fois que 60 pièces, dont 55 bonnes, au lieu de 80.
Avec cette formule du calcul du TRS, on aura donc ;
TRS = 55 / 80 = 68.75%
Les indicateurs de performance
Il est alors inutile de rappeler que les formules précédentes sont largement trahies par les limites de leur périmètre de mesure.
Heureusement, le Taux de Rendement Synthétique (TRS), admet une formule beaucoup plus complète qui fournit une vision synthétique, approfondie et sévère de la performance globale d’un atelier, en un seul chiffre.
Cette formule très utilisée en entreprise utilise trois indicateurs normés par l’AFNOR, le Taux de Disponibilité Opérationnelle (TDO), le Taux de Performance (TP), et le Taux de Qualité (TQ).
La disponibilité d’un outil de production est un indicateur de performance qui permet de mesurer tous les arrêts détectés du moyen qui affectent son rendement.
Aussi l’ensemble de ces évènements qui stoppent la production peuvent être des arrêts de causes internes, appelés les temps d’arrêt propres, dépendants de la machine (réglage, pannes, …) ou des causes externes, les temps d’arrêt induits, ne dépendants pas de la machine (absence de personnel, défaut d’énergie, manque matière…).
De manière générale, le taux de disponibilité est donc égal au rapport entre le temps de fonctionnement du moyen et son temps d’engagement (temps requis).
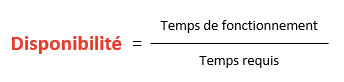
Une fois le temps de fonctionnement connu (temps requis – temps d’arrêt), il existe bien souvent des écarts de cadence entre la performance réelle et la performance nominale ou théorique.
Finalement cette performance réelle se calcule en faisant le rapport entre le temps net (temps pendant lequel le moyen fonctionne à la cadence nominale) et le temps de fonctionnement du moyen.
La performance cherche à comparer la quantité réellement produite, par rapport à la quantité maximale (ou nominale) qu’il aurait été possible de réaliser pendant le temps d’engagement de fonctionnement du moyen.
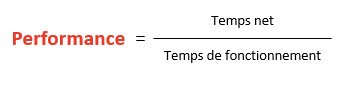
Après avoir déduit les temps d’arrêt non planifiés (taux de disponibilité) et les écarts de cadence (taux de performance), il arrive bien souvent que la quantité produite diffère de la quantité attendue.
Mais la différence s’explique par la production de mauvaise qualité. Ces rebuts, souvent appelés « non-qualité » sont la différence entre la quantité réalisée et la quantité bonne. Ils identifient le taux de qualité.
Le taux de qualité se calcule soit par les temps soit par les quantités :
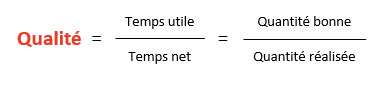
Formule de calcul du TRS par les indicateurs de performance
Le moyen le plus utilisé et le plus précis pour calculer le TRS d’un moyen de production est donc d’utiliser ces trois indicateurs de performance : taux de disponibilité, taux de performance et taux de qualité. Et ce pour plusieurs raisons.
Premièrement, l’introspection nécessaire du moyen de production pour le calcul de ces indicateurs met bien souvent en évidence d’éventuelles causes de non-TRS, et pas seulement d’en calculer le résultat et l’impact sur la production.
C’est une véritable analyse de l’atelier, non seulement de l’outil de production mais également des autres ressources nécessaires au bon fonctionnement de ce dernier (ressources humaines, énergies, matières, …).
Une fois les causes de non-TRS identifiées, il est alors possible de mettre en place des plans d’actions pour optimiser la production. C’est donc un véritable outil d’investigation efficace pour quiconque souhaite améliorer l’efficacité d’une usine.
Enfin, pour calculer le TRS d’un outil de production via les indicateurs, il suffit de réaliser le produit des trois taux préalablement définis.
TRS = Taux de Disponibilité x Taux de Performance x Taux de Qualité
Exemple de calcul du TRS :
Afin de mieux comprendre la marche à suivre pour le calcul du TRS, prenons un moyen de production classique, avec un temps d’ouverture de 8h à 17h, et une cadence nominale de 100 pièces / heure.
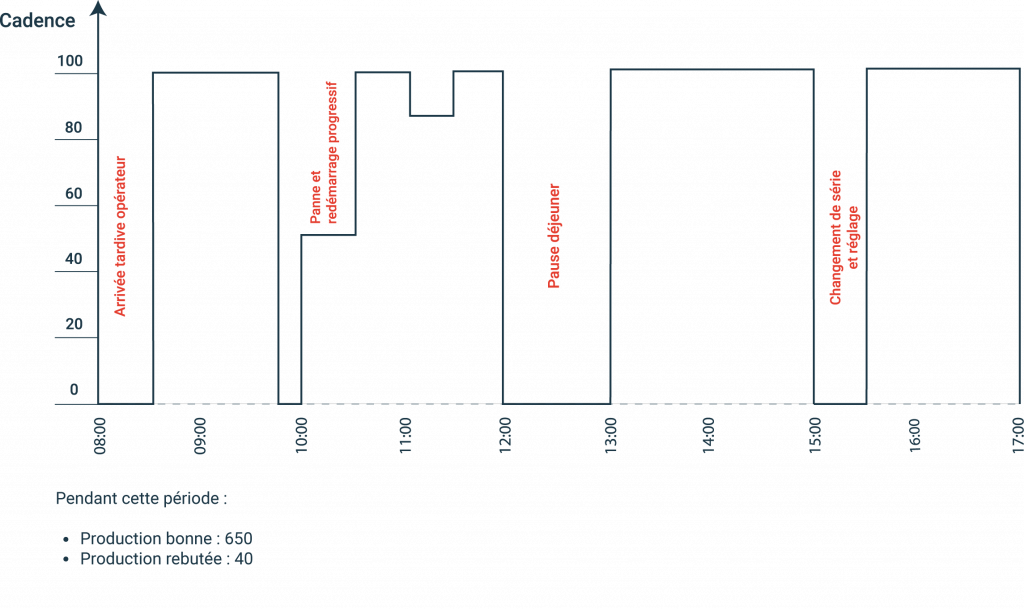
1. Nous commençons par calculer le taux de disponibilité :
Rappel :
Disponibilité = temps de fonctionnement / temps requis
Avec
- Temps de fonctionnement = temps pendant lequel le moyen a réellement produit
- Temps requis = Temps pendant lequel le moyen est engagé pour produire
On a donc dans notre cas :
Temps requis = Temps d’ouverture – pause déjeuner
= (8 x 60) – (1 x 60)
= 420 mn
Temps de fonctionnement = Temps requis – (arrivée tardive opérateur 30mn + panne 10mn + changement de série et réglage 30mn)
= 420 – (30 + 10 + 30) = 420 – 70 = 350 mn
Taux de disponibilité
= 350 / 420
= 0.8333
et donc 83.33%.
2. Ensuite, nous calculons le taux de performance :
Rappel :
Performance = temps net / temps de fonctionnement
Avec
- Temps de fonctionnement = 350 mn (voir calcul plus haut)
- Temps net = temps de fonctionnement – écart de cadence
On a donc dans notre cas :
Temps de fonctionnement = 350 mn
Temps net = 350 – (50 pièces /h de 10h à 10h30 + 20 pièces /h de 11h à 11h30)
= 350 – {(50 x 0.5 x 0.6) + (20 x 0.5 x 0.6)} = 350 – (15 + 6) = 329
Taux de performance
= 329 / 350
= 0.94
et donc 94%.
3. Enfin, nous calculons le taux de qualité :
Rappel :
Qualité = temps utile / temps net
Avec
- Temps net = 329mn (voir calcul plus haut)
- Temps utile = temps net – temps passé à faire de la non-qualité
On a donc dans notre cas :
Temps net = 329 mn
Temps utile = 329 – (40 x 0.6)
*(Les pertes dues à la non-qualité représentent une perte de temps utile de 40 x 0.6 = 24 minutes)
= 329 – 24 mn
= 305 mn
Taux de qualité
= 305 / 329
= 0.927
et donc 92.7%.
Rappelons que le TRS est égale au produit de ces trois indicateurs
TRS = Taux de Disponibilité x Taux de Performance x Taux de qualité
Dans notre cas,
le taux de rendement synthétique =
= 0.83 x 0.94 x 0.92
= 0.72
et donc 72%
A savoir :
Chacun des trois taux qui composent le TRS peut s’exprimer en ratio de temps mais également en ratio de pièces.
La Disponibilité

La Performance

La Qualité
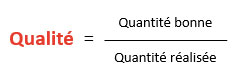
Logiciel MES Aquiweb et TRS
Le logiciel MES Aquiweb favorise l’augmentation du TRS en digitalisant les ateliers de production.
En effet, le TRS est un ratio entre plusieurs facteurs de performance industrielle qui doivent non seulement être connus, mais surtout analysés. Mais la connaissance de ces indicateurs se fait à travers une collecte précise et régulière de l’ensemble des données de production, telles que la quantité de rebut, la cadence de production, les arrêts et leurs causes etc…
Cette collecte est contraignante parce que réalisée manuellement et approximativement. Cependant, de nombreuses entreprises décident de digitaliser et d’automatiser ces aspects de collecte et d’analyse des données de l’outil de production, c’est un élément important de l’industrie 4.0.
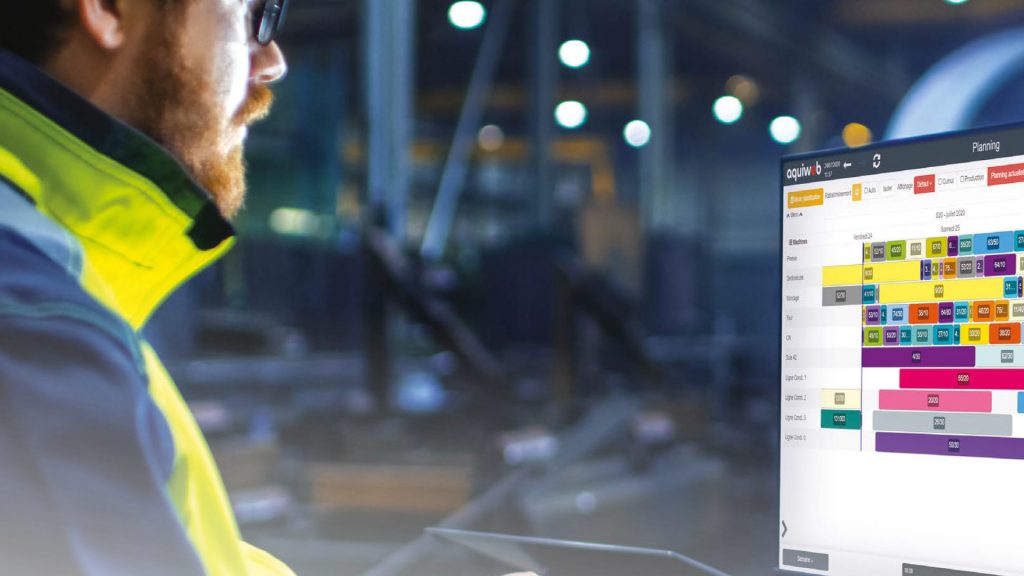
Le MES (Manufacturing Execution System) Aquiweb est un logiciel pour optimiser la production qui collecte les données du terrain en temps réel auprès des équipements (grâce à des IIoTs) et auprès des hommes (terminaux). D’autre part, après un travail d’analyse, il accompagne les managers et responsables dans des démarches d’amélioration continue, analyse Pareto, SMED, 5S etc…
Libérer du temps aux managers et opérateurs
Finalement côté opérateur, le logiciel MES Aquiweb accompagne l’augmentation du TRS par une digitalisation et une simplification du processus de fabrication. Mais aussi par la mise à disposition de l’opérateur d’une vision instantanée de sa performance.
Alors que traditionnellement ces données doivent être collectées, puis consolidées, vérifiées et analysées à « la main », le logiciel MES Aquiweb digitalise l’ensemble de ces étapes et propose des indicateurs pour mieux suivre la performance globale de l’atelier.
Il collecte automatiquement et en temps réel les données nécessaires au calcul du taux de performance, taux de disponibilité opérationnelle, et taux de qualité. Alors les données mettent en avant des causes de perte de performance de l’atelier, permettent d’optimiser les ressources utiles à la production et tout cela, en visant le « zéro papier ».
Finalement, le logiciel MES Aquiweb libère les managers en leur offrant des données consolidées et peuvent ainsi se consacrer à la gestion et à l’animation de leurs équipes plutôt qu’à la collecte des données (gain minimum de 2h par jour).
Ainsi, Aquiweb accompagne les opérateurs en dématérialisant les opérations de productions : TRS, suivi, traçabilité, documentation, qualité, matière, planning…
Tous les industriels qui utilisent Aquiweb constatent une augmentation minimum de 5 à 20 points de TRS.